GREEN INNOVATION
TO A SUSTAINABLE FUTURE
GREEN INNOVATION
TO A SUSTAINABLE FUTURE
Climate Strategies
To achieve its GHG emission reduction target, the Group has developed climate strategies to effectively reduce GHG emissions from its asphalt business in Thailand, while also aiming to expand its coverage in the future. There are six main climate strategic projects under the climate strategies, as follows:
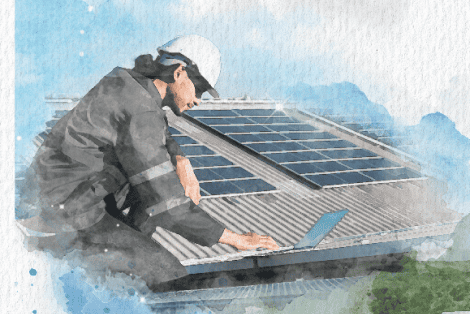
SOLAR ROOF
The Group plans to make substantial investments in renewable energy through installing solar rooftops at its manufacturing plants in Thailand. This project serves as a step towards achieving energy independence. The solar rooftops will harness sunlight to generate electricity, reducing reliance on conventional power sources which resulting in more sustainable energy mix.
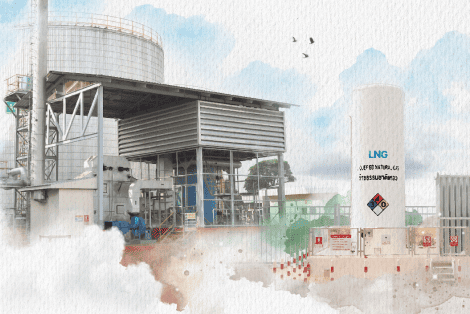
FUEL-SWITCHING TO LNG
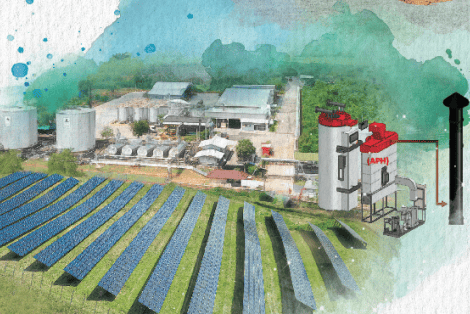
ELECTRICAL HOT OIL BOILER WITH SOLAR POWER
The Group plans to reduce GHG emissions through replacing its diesel hot oil boiler unit with an electrical hot oil boiler unit. By using electricity for the heating system in the production process, the Group can eliminate GHG emissions associated with traditional heating methods that use diesel as a fuel source. To further reduce reliance on electrical grid, the Group will also invest in solar power to generate solar energy for the electrical hot oil boiler

SPECIALIZED LOGISTIC PARTNERS
As part of the supply chain optimization initiative, the Group will be able to reduce part of its Scope 1-2 GHG emissions by leveraging like-minded specialized logistic partners to effectively and efficiently manage product deliveries and associated emissions.
The Group recognizes that logistic-associated emissions of the partners will fall under indirect Scope 3 GHG emissions of the Group, and confirms that the Group will do everything possible to reduce such emissions by means under its control, e.g. by selecting logistic partners that can service with electric or fuel-efficient trucks.
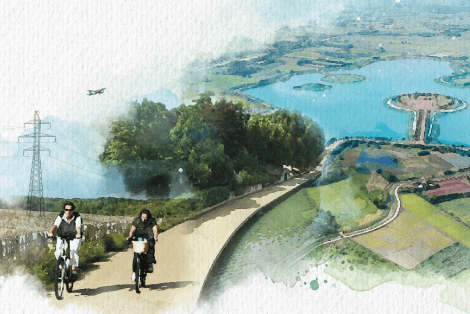
AFFORESTATION
For the past several decades, the Group has implemented various afforestation projects with the aim to increase and restore forest areas. In continuation with this aim, a key afforestation strategic project was developed as a major step forward, starting in 2024 and completed by 2033 with the planting of 120,000 trees. The annual GHG emissions reduction from the project is estimated to be 1,140 tCO2e per year. While afforestation plays a vital role in neutralizing the Group’s residual GHG emissions in supporting Thailand’s NDC , it will not be accounted for in the GHG emission reduction targets for 2030.
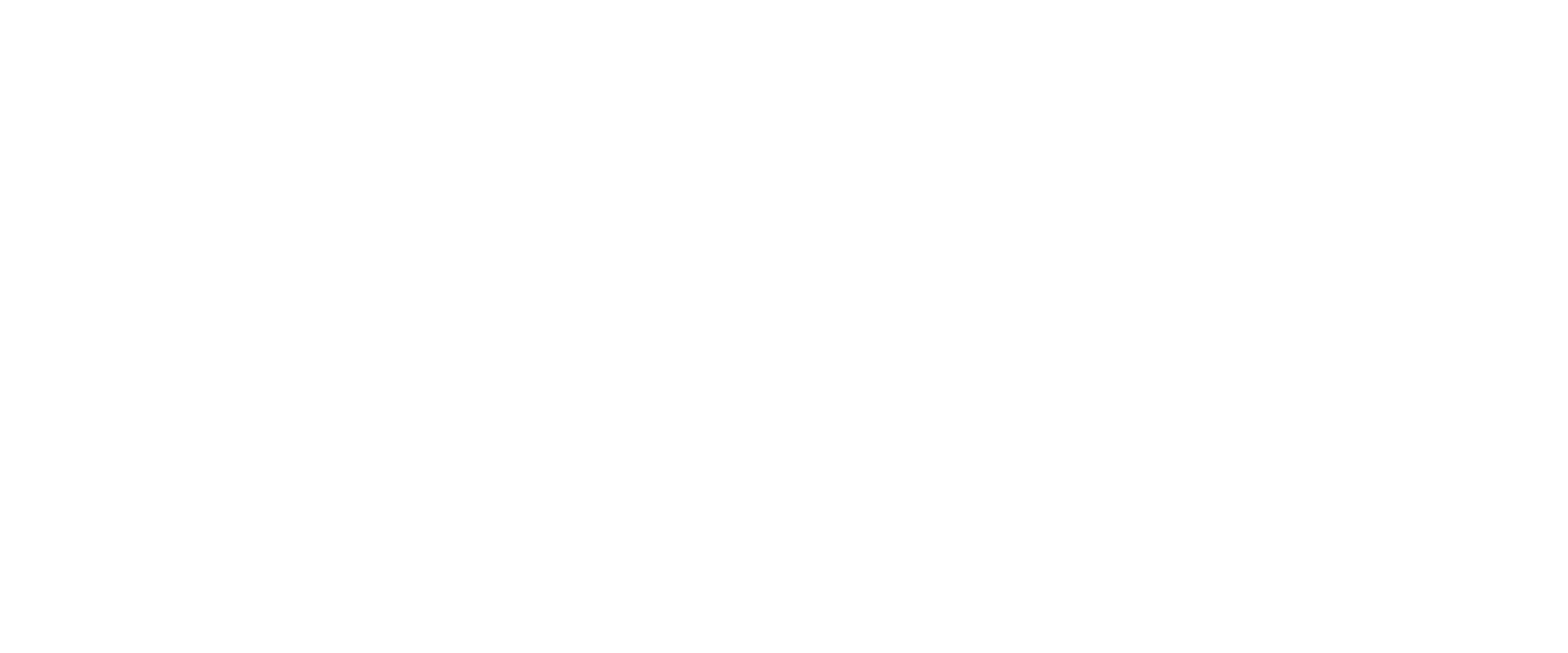
Green Solution Benefits
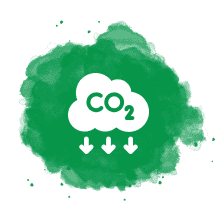
Carbon emissions are reduced when compared to a conventional hot-mix binder course overlay
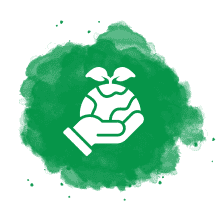
Protect human and environmental health.
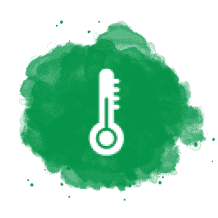
Energy use at the hot-mix plant is reduced
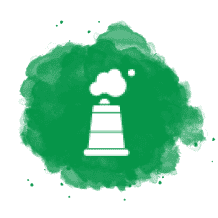
Smoke and VOCs at the jobsite are reduced
Green Solution Applications
MICRO-SURFACING / FIBROSEAL
Micro-surfacing / Fibroseal is the process of enhancing the aging surfaces that are slipping, and unsafe, making them stronger and improving the friction performance as well as the skid resistance of road surfaces. This is achieved by applying a new surface coating using polymer-modified asphalt emulsion mixed with course materials, adding the extra filler, additives, and synthetic fibers for flexibility, durability, high tensile strength, and resistance to various weather conditions. It can prevent water leakage into the surface layer and is suitable for all road surfaces such as expressways, elevated roads, river bridges, and various underground passages.
- Helps reduce CO2 emissions by at least 70% compared to improving surfaces with new asphalt concrete overlays.
- Extends 5-7 years the lifespan of asphalt concrete roads.
- Between 2019 and 2023, Tipco Asphalt supplied 18,400 tons of polymer-modified asphalt emulsion for use in micro-surfacing / Fibroseal up to 14 million square meters. This helps reduce FOA fuel consumption up to 8 million liters.
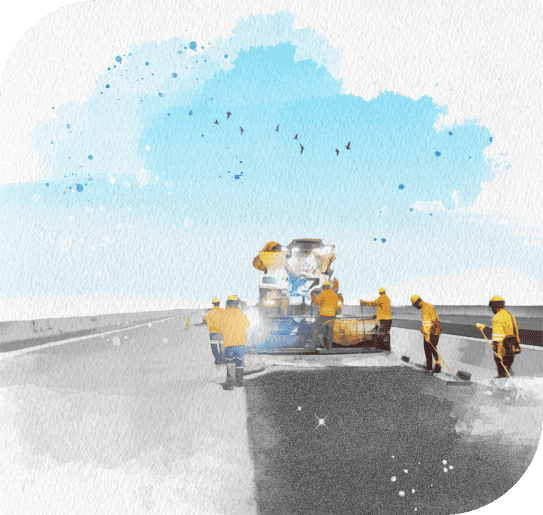
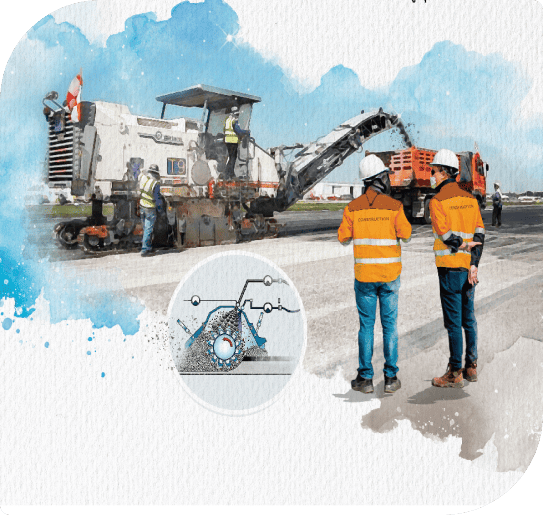
PAVEMENT IN-PLACE RECYCLING
This is a method of improving damaged existing pavements by excavating, milling, and improving the quality of existing pavement to meet the specifications. This may involve adding new aggregates to improve the grading and adding specific fillers such as cement, lime, fly ash, or asphalt emulsion before recompacting the existing pavement and surface overlaying with the new asphalt concrete. This Pavement In-place Recycling method can save time and reduce energy consumption in transportation as well as reliance on natural resources.
It can reduce CO2 emissions by up to 80% compared to the conventional method of milling off the existing pavement and replacing it with new materials.
- Can be used on all types of roads, intercity roads, expressways, and superhighways.
- Mostly used for pavement rehabilitation
- Asphalt emulsion used in pavement rehabilitation can be recycled in the future.
COLD MIXED ASPHALT (CMA)
Cold Mix Asphalt is the mixing of aggregates with the asphalt emulsion CMS-2h. The mixing process can be done at normal temperature without heating, unlike hot mix asphalt concrete, which saves fuel and energy costs, reduces combustion, and reduces CO2 emissions. Cold Mix Asphalt can be used for road resurfacing and general surfacing work.
- Reduces odors and hydrocarbon volatiles at the work site by up to 90%.
- Reduces CO2 emissions during the production process by 100%.
- Between 2018 and 2022, Tipco Asphalt supplied 484,000 tons of asphalt emulsion to produce Cold Mix Asphalt, which helped to reduce FOA combustion by 2.66 million liters.
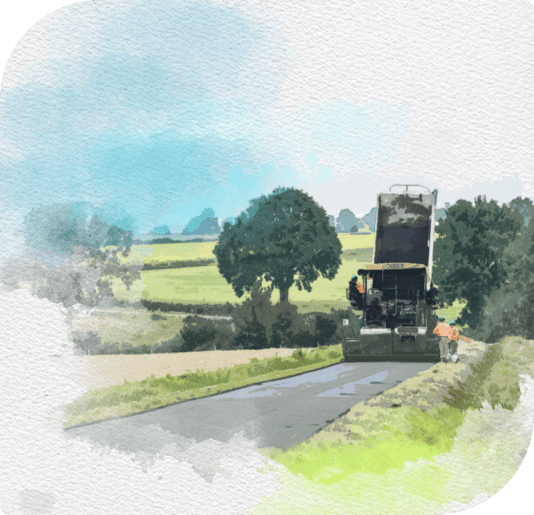
Green Innovation
to a sustainable future
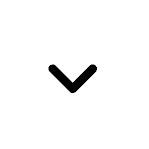
The Green Future
Tipco Asphalt is committed to developing new products and solutions that are environmentally friendly and help Thailand achieve its climate goals. We are researching and developing asphalt cement from natural plants or Bio-binders to reduce CO2 emissions into the atmosphere. We are also developing renewable energy from plants and Biomass to reduce the problem of long-term pollution from fossil fuels.
WARM MIX ASPHALT
Warm Mix Asphalt is a new technology in asphalt concrete production, offering several advantages compared to traditional Hot Mix Asphalt. It uses 10 to 40 degrees Celsius lower than typical temperatures in production, which reduces energy consumption and decreases CO2 emissions during both production and application pavement. This technology maintains the performance and durability of road surfaces, preventing the formation of rutting. Additionally, Warm Mix Asphalt is easy to work with due to lower temperatures during paving and compaction, ensuring safety for construction workers and the public. It is considered a cost-effective and environmentally friendly option for contemporary road construction and maintenance.
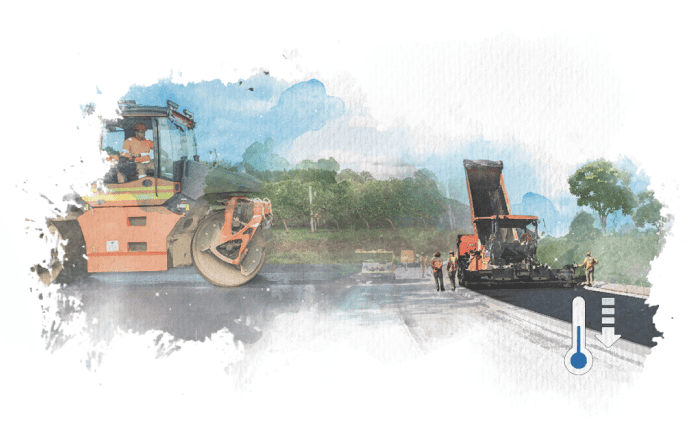
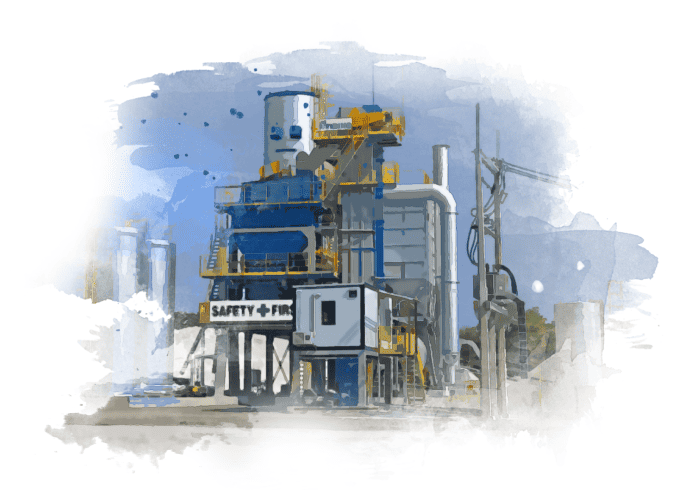
ASPHALT HOT IN-PLANT RECYCLING
The rehabilitation of existing asphalt concrete pavements involves recycling the material from old asphalt concrete surfaces. This process starts by milling the existing pavement surface and then reintroducing the material through a new production process at the central plant. By heating the reclaimed asphalt material and enhancing the quality of the existing asphalt cement properties, this method proves environmentally friendly. It reduces the need for new raw materials, minimizes waste, and conserves resources. Moreover, using Asphalt Hot In-plant Recycling in rehabilitation helps save energy, lower CO2 emissions, and contributes to sustainable road development economically and environmentally.
REJUVENATOR
Rejuvenator or Asphalt Recycling Agents are hydro-carbon compounds that can be directly extracted from natural plants to replace distillation from crude oil and are beneficial for Asphalt Cement in improving the flexibility, strength, and durability of reclaimed asphalt concrete, allowing it to be continuously reused. It is a sustainable alternative for restoring deteriorated asphalt pavement without the need to waste energy transporting new materials from elsewhere to work, helping to reduce carbon dioxide emissions and prevent air pollution, thus being environmentally friendly. It provides economic and social benefits by extending the lifespan of existing structures
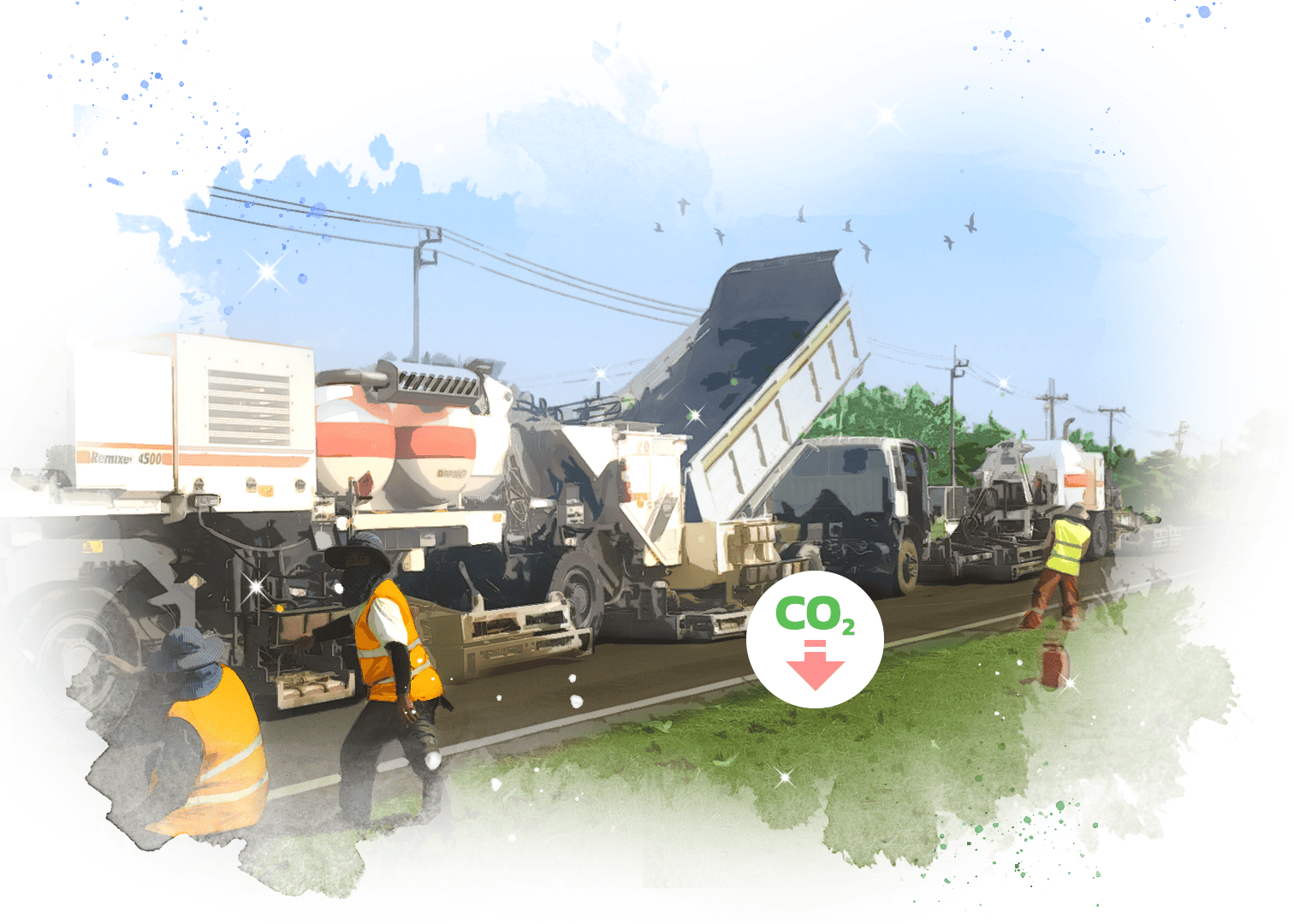
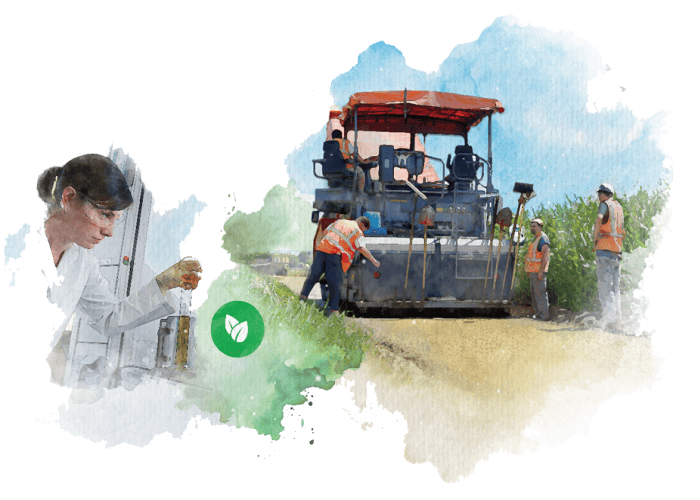
BIO-BINDERS
BIOMASS
Biomass is a renewable fuel derived from natural plants, which can be continually replanted. Most raw materials come from agricultural and plant processing industries, such as wood scraps, corn husks, bagasse, palm kernels, fruit peels, etc., from various factories such as sugar mills, biomass power plants, rice mills, paper mills, and flavor powder factories. These leftover scraps undergo processes such as grinding and drying to eliminate moisture before being used as an alternative fuel to provide heat in the production process of a Hot-mix asphalt concrete plant, which can reduce the use of fossil fuels by more than 40%.
The use of biomass is therefore a way to utilize agricultural by-products to create added value, reduce waste, and minimize environmental impacts. At the same time, it promotes the sustainable use of renewable energy.
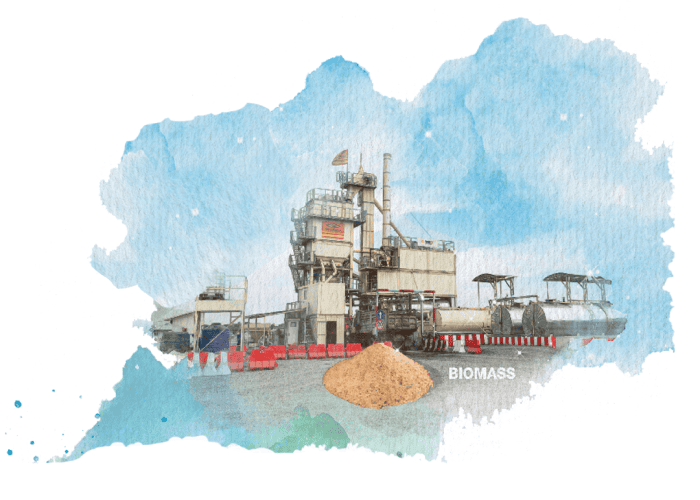